We had originally planned to do a sod roof (just as we had originally planned to build a round house). In the end, metal roofing seemed to fulfill more---though definitely not all---of our often conflicting project goals. The advantages include ease and speed of installation, longevity and low maintenance of the material---and the fact that snow might tend to slide off a metal roof far more easily than other materials, even at our low 1:12 pitch. A sod roof, while it would moderate inside temperatures, use greener (so to speak) materials, and help the house blend with its surroundings, would have required us to engineer for a far heavier roof and snow load, and would have taken much longer to install.
Next step was to install fascia boards, eaves, and soffits.
Joe rigged a kind of cantilevered scaffolding out of 2X4s (Brian's idea, I believe?).
![]() |
![]() |
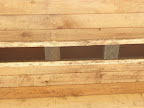
![]() |
Now to get sixteen 30-foot panels onto the roof. Levers and pulleys would have helped---large mechanized equipment even more. As it was, we fortunately had the power of son Ian to help. Suffice it to say that it took a lot longer---and was far more painful---to get the panels onto the roof than it took to line them up and secure them. It was what you call a character-building experience. Screwing them down seemed easy after that.
The roofing came with these nifty foam inserts to plug up the peaks of the roofing panels.
![]() |
The metal roofing hangs over the plywood substrate by a couple of inches. This is so gutters can be tucked under the sheathing, so that water will flow directly into them rather than down the fascia boards.
![]() |
1 comments:
So cool. :) Nice to see how it's coming along.
Post a Comment